Belt conveyor Principle
- Share
- Issue Time
- Nov 22,2021
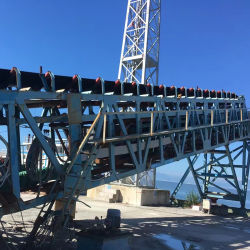
Principle of operation:
A belt conveyor is simply an endless strap of flexible material stretched between two drums and supported at intervals on idler rollers. When the drum rotated by the driving motor, the belt will move with roller due to frictional resistance, there by the material placed on the belt will be transported from one place to other.
Majority of belt conveyors are equipped with flat belts. Troughing the belt or fitting sidewalls will increase the carrying capacity. Fitting the transverse slats or texturing the surface of the belt will help to operate the belt conveyor for steep inclined application. The end of the conveyor where transported material is loaded is termed as ‘tail end’ or ‘feed end’ and the other end, from which the load is discharged, is called as ‘head end’.
Belts: Belts may be flat or fitted with a pattern of cleats or flights molded into its surface to reduce the tendency for the conveyed material to slip. The belts may be constructed with vertical sidewalls, which may be supported by transverse slats to operate much steeper incline than the normally accepted. Two methods are employed i.e. vulcanized splice and mechanical fasteners at the ends of the belt to make the belt endless. The expensive vulcanized splice gives a much stronger and longer lasting joint. The cheaper mechanical fasteners tend to restrict the working conditions of the belt.
Idlers: The carrying capacity of the flat belt is increased by modifying the cross sectional profile of belt so that it forms a trough. This is achieved by troughing idler, which consists two to five rollers.
Drive arrangements: The drive may be at either end of the conveyor, but prefers to drive the head end drum since the smallest amount of belt being subjected to the maximum tension. The effectiveness of the conveyor drive is dependent upon the difference in tension between the ‘tight side’ and the ‘slack side’ of the belt, the friction between the belt and the drive drum and the angle of wrap or arc of contact of the belt to drum. The power that can be transmitted from the driving drum to the belt is limited by the point at which the belt begins to slip. In order to increase the power either coefficient of friction to be increased by applying a rubber lagging to the surface of the drum or to increase the angle of wrap by ‘snubbing’ the drum or by providing a multiple drive.
Belt slip: In the belt drive there will inevitably be a certain amount of belt ‘creep’ resulting from the varying tension in the belt as it passes around the drum. The term ‘creep’ refers to the relative movement between the belt and the surface of the drum that happens as the stretch in the belt decreases with the reduction in tension. The arc of the drum surface over which creep occurs will tend to increase as the tight side tension increases, for example as a result of increasing the load on the belt, and if the ‘angle of creep’ approaches the ‘angle of wrap’ the belt will be on the point of slipping. For this reason that a certain inherent tension should be maintained, even in the slack side of the belt.
Belt tensioning: The needed tension can be provided in a number of ways by suitable arrangement like pulling back the tail drum or idler pulley and also by providing ‘drop-weight’ or ‘gravity take-up’ device. Hydraulically or electrically powered automatic take-ups are also available which relay on a load-sensitive device to move the tensioning pulley in response to change in operating conditions of the belt.
Belt cleaners: When transporting bulk materials that have the tendency to stick to the surface of the belt, the belt conveyors will be equipped with some kind of cleaning technique at the head end to minimize the build-up of material on snub pulleys and return idlers. Theses cleaning methods are such as rotary brushes or scrapper blades of steel or rubber, which may be spring loaded or counterweighted to bear against the surface of the belt.